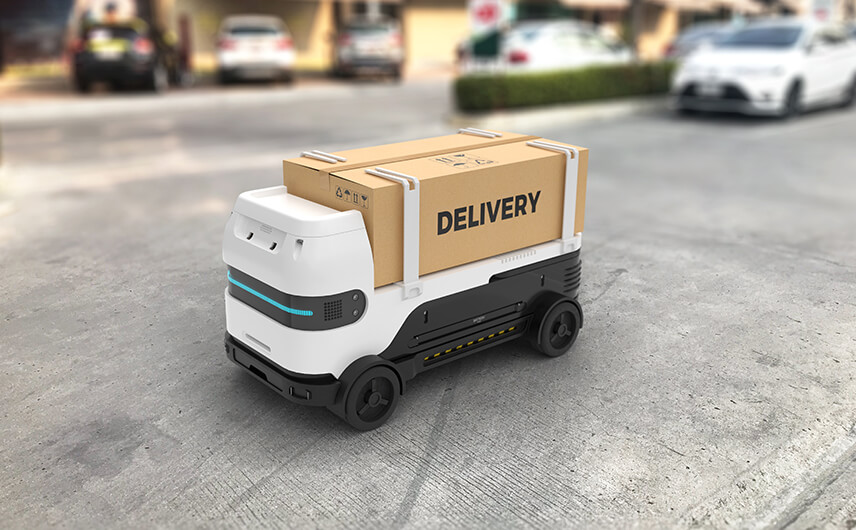
Over the past year and a half, the United States and China have engaged in a trade war that has unleashed volley after volley of reciprocal import tariffs from the world’s two largest economies, driving up duties on a wide range of items, including agricultural goods.
For established US importers and exporters of perishable foods and other refrigerated (reefer) cargoes, fluctuations in trade policy between the US and foreign buyers and sellers have long necessitated a diversified and nimble supply chain strategy. Nevertheless, the current trade war is creating unique challenges, according to a senior supply chain executive from a major US-based food company. The firm trades and sources products around the world, as well as exporting food from the US and Canada to China.
In June, China banned meat imports from Canada, charging that a feed additive (ractopamine) was detected in Canadian pork shipments and veterinary certificates for the livestock were fraudulent. Guy Saint-Jacques, Canada’s former ambassador to China, said Beijing was essentially using phytosanitary concerns as an excuse to block exports.
According to the food company executive, non-tariff barriers such as animal health/disease are the leading challenge to accessing foreign markets, followed closely by geopolitical issues. Russia, for example, has blocked US poultry imports for the past decade over similar phytosanitary issues.
“What do you do? You shift, and we’ve been doing this for a long time. The name of the game for us is diversification,” the executive told JOC.com.
Unlike prior trade spats, which tended to flare up and then dissipate, returning the market to “normal” operating conditions, the current tensions between the US and China stand out because there’s been a steady escalation over the past 18-plus months, with no end in sight.
“The uncertainty of markets opening and closing is definitely an issue for us,” the executive explained, adding that production in the US and Canada has been severely disrupted. And with so much of the firm’s product on the water at any given time, when there’s an abrupt change to tariffs, the impact is that much more significant, as the company cannot simply redirect that cargo elsewhere.
“You’re forced to find the best alternative for a bad situation,” he said.
Moreover, some food products that the company exports are specific to a particular market or markets, such as certain animal parts the company ships to China. “There aren’t a lot of markets in the world that eat chicken feet, so if you can’t sell your chicken feet to China, then you’ve got a real problem. Those kinds of disruptions can cause you to lose a lot of money really fast,” he said.
The executive said the concept of a trade war — use of restrictions such as tariffs and quotas to damage another country’s position in the global marketplace — has been around for decades, and the latest conflict, although more intense than some, has only reinforced the need for a diversified sourcing and supply chain strategy.
“There has been a trade war going on for 30 years, but now there’s a broader impact across more commodities,” he said.
Mutual adaptation
Similar to cargo owners, ocean carriers are often tasked with responding to changing market conditions over which they have little or no control. The food company executive said some are performing better than others in the current tariff environment.
“We have to keep product moving, and we selected a particular carrier because they were more flexible,” he said. “Flexibility has become a competitive advantage for some ocean carriers.”
Despite what some have described as a commoditization of container freight services over the past several years, his company looks for more than just the lowest rate when choosing a carrier. “It’s about who you have relationships with, or the carrier’s mentality. Some are good operators and they’re nimble,” he said.
As a result, the company is “definitely selecting carriers more carefully now than in the past, especially for markets that are more affected [by the trade war] than others.”
The executive said that although the market has “moved beyond the initial shock” of widespread carrier consolidation in 2016 and 2017, his firm is “more diligent about who we’re doing business with and what strings they’re on. You have to work with the three major [east-west vessel sharing alliances], and you’ve got to make sure you’re spreading your freight among those strings — not just the carriers — and we’ve changed some of our processes to account for that.”
US food importers/exporters are also facing disruption in the form of insufficient staffing in the Department of Agriculture’s inspection services, particularly at inland locations. Although the problem has been somewhat less pronounced of late thanks to softer volumes over the summer, “It’s still a big issue for us,” he said.
Meanwhile, the pending implementation of the International Maritime Organization’s (IMO's) low sulfur-fuel regulation is seemingly attracting less attention these days, according to the executive, even though there are some signs that the industry may not be fully prepared to comply with the new rule when it takes effect on Jan. 1, 2020.
“It’s eerily quiet right now,” he said, despite reports of scrubbers taking longer to install on vessels, or scrubbers not being ready and available for installation. “We also don’t know if the proper fuel is going to be in the right place or not.”
That poses problems for vessels that cleaned their tanks expecting to refuel with low-sulfur diesel, only to find that the fuel is unavailable.
Improving freight flows
Due to the time- and temperature-sensitive nature of their products, reefer shippers are among the most affected by congestion at cargo terminals, but utilizing inland ports where possible can help keep cargo moving. South Carolina Ports Authority’s Inland Port Greer and Georgia Ports Authority’s Appalachian Regional Port (ARP), which opened in August 2018, are two worthy examples, the executive said.
Logistics complexes such as KC SmartPort in Kansas City, Missouri, provide a similar solution in the form of transloading, according to Walter Kemmsies, economist and chief strategist at JLL. Four interstate highways and five Class I railroads intersect at KC SmartPort. When refrigerated imports move via rail from ocean ports to complexes such as KC SmartPort, it creates opportunities for exporters of US beef, poultry, pork, and other perishable foods that need empty reefer containers. In addition, it avoids the transloading of 53-foot trailers into 40-foot containers at or near heavily congested port gateways.
In some cases, however, transloading at or near ports is unavoidable.
In the Los Angeles area, for example, more transload facilities are being sited on large tracts of land — up to 50 acres — where import/export containers can be processed and cargoes transloaded into 53-foot trailers more efficiently. It’s also a way to minimize container detention and demurrage charges and maintain a consistent flow of freight through distribution centers, says Kemmsies.
Up the coast in Northern California, the completion of a refrigerated transloading and distribution center last summer is contributing to increased volumes of reefer cargo at the Port of Oakland. The $90 million facility was funded primarily by Cool Port Oakland LLC, a joint venture comprised of Lineage Logistics and Dreisbach Enterprises, with rail infrastructure partially funded by the port via state grants.
In particular, continued strong consumer demand in Japan and South Korea for US reefer exports — along with more robust farm production in the US — helped the port achieve a 20 percent increase in exported reefer container volumes from Aug. 1, 2018, through July 31, 2019, compared with the previous 12-month period, according to a Port of Oakland spokesperson.
Cold chain investments by port partners, including Dreisbach, PCC Logistics, and Unicold Corporation, are also contributing to growing reefer cargo volumes, the spokesperson said.
While importers/exporters moving hundreds of thousands of containers through major port gateways such as the Port of New York and New Jersey and the Los Angeles-Long Beach complex generally have higher margins to play with thanks to their sizeable volumes, smaller beneficial cargo owners (BCOs) feel the impact of cost increases more acutely.
One way in which smaller reefer shippers can mitigate total costs is by using other marine gateways where costs for inland trucking, distribution, cold storage, and labor are considerably cheaper, but that still offer the necessary transportation links and distribution networks to get product where it’s needed.
Future development
At the same time, ports are looking for ways to improve their operations to support reefer BCOs.
At the Port of Long Beach, for example, dedicated specialists help assure reefer containers are handled properly and get immediate attention if maintenance or repairs are required, explained Don Snyder, acting managing director of commercial operations at the port.
The port is continuing to invest in infrastructure to facilitate cargo flow, including adding more capacity to terminals and expanding its on-dock rail capabilities. Snyder also praised “a darn good freight forwarding community” and “expanding cold storage capacity” for helping support reefer BCOs.
Attention is still required in several areas though, says Snyder, particularly in landside connections between railroads, truckers, and terminal operators.
“There’s no financial relationship” between these parties, “so we are continuing to work on business practices, process improvement, and operational excellence,” he said.
At neighboring Port of Los Angeles, marketing manager Marcel Van Dijk said the goal is to provide premium handling to all cargo regardless of type, but he conceded reefer cargo requires “a little more infrastructure.”
For example, all reefer containers are placed on chassis, rather than stacked on top of each other, and then moved to a dedicated area where they are plugged in. If the reefer container is handled at one of the port’s automated terminals, it’s placed in the reefer rack instead of on a chassis. The automated terminals — one at the Port of Los Angeles, the other at the Port of Long Beach — also work on an appointment system for truckers, which means reefer boxes are pulled from the rack and ready to go at the scheduled pickup time.
As for cold storage capacity, KPAC Cold Storage is said to be planning to expand its footprint in the Los Angeles-Long Beach port area.
In addition, the Port of Los Angeles is also working to speed up turn times for trucks, which at 83 minutes on average across all terminals, “is not that good,” Van Dijk conceded. To that end, terminals are also expanding their appointment systems and looking for ways to make those systems more user friendly for truckers.
According to Van Dijk, the GE Port Optimizer information portal has the potential to help further improve cargo visibility and handling at the port. Approximately 50 BCOs are beta testing the portal currently and the platform should be fully operational by the end of the year. The plan is to provide some “general information” free of charge, with other information available via a subscription model, Van Dijk said.
“BCOs can put info into the portal as soon as they have a booking number and a container number. They know when the container is loaded at the foreign port and the ETA at the Port of Los Angeles. If there are any changes, those changes are viewable in the portal right away. Once the container arrives in LA, the BCO can see when it’s available for pickup,” he said.
Kemmsies acknowledged the potential benefits of the GE Port Optimizer platform but said technological advancements alone cannot make up for the infrastructure, planning, and network design shortcomings that exist in varying degrees throughout the entire global supply chain.
According to Kemmsies, the changes that will be needed are not small renovations or upgrades. Rather, they are fundamental changes more akin to the shift from coal-fired plants to natural gas and renewable energy.
“We’ve basically hit a tipping point,” he said, and it’s a problem that’s been in the making for a long time. “In the end, we need to make infrastructure investments, and we also need to change the way we’re doing things.”